- Massive Impact: The metals industry is a significant contributor to pollution. Steel accounts for 7-11% of global CO₂ emissions, and aluminum contributes an additional 2%. Production also significantly impacts water and land, with issues like acid mine drainage and toxic "red mud" waste.
- Production Matters: How a metal is made is the biggest factor in its carbon footprint. For steel production, the coal-based BF-BOF process is highly polluting, whereas the scrap-recycling EAF process is over 75% cleaner. For aluminum and copper, recycling uses 85-95% less energy than primary production.
- Decarbonization solutions exist, with key technologies being deployed. These include maximizing recycling, utilizing green hydrogen to replace coal in steelmaking (HYBRIT project), developing inert anodes for aluminum production to eliminate process emissions, and retrofitting older plants with Carbon Capture and Utilization Systems (CCUS).
- PCF is a key metric for any business using metals. The most important data point to get from a supplier is whether the metal was made via a primary (from ore) or secondary (recycled) route.
- Regulation is Forcing Action. The EU's Carbon Border Adjustment Mechanism (CBAM) creates a direct financial cost for the carbon in imported steel and aluminum. Transforming PCF measurement from a voluntary action into a competitive and financial necessity for businesses in global supply chains.
The unseen carbon in our industrial backbone
Steel, aluminum, and copper are foundational materials of the modern world. They provide the skeleton for our cities, the framework for our infrastructure, and the core of our transportation and energy systems. Their strength and versatility have made them integral to global progress.
This reliance on metals comes with a large environmental cost. The metals industry is a major source of pollution and a primary driver of climate change. The iron and steel industry alone is responsible for 7% to 11% of the world's total carbon dioxide (CO₂) emissions.
When combined with other major metals, such as aluminum, which contributes an additional 2% of human-caused emissions, the scale of the challenge becomes clear.
Let’s explore the full environmental impact of key industrial metals, including their effects on water and land.
The environmental impact of metal production
The environmental impact of metal production goes far beyond carbon emissions. A comprehensive review reveals a significant impact on the planet’s air, water, and land.
To effectively manage the sustainability of any product containing these materials, it is essential to understand the complete footprint.
The size of the metals industry makes its climate impact a global issue.
The massive carbon footprint of steel production stems from its deep-rooted dependence on coal. For aluminum, the story is about electricity; primary production is one of the most energy-intensive industrial processes on the planet.
These impacts are not limited to emissions. The metal lifecycle has other severe effects on natural systems.
Water Consumption and Pollution
Metal manufacturing utilizes a significant amount of water for cooling and cleaning purposes. This high consumption strains local water resources. Furthermore, if not treated properly, the discharged water can pollute local ecosystems with heavy metals, chemicals, and thermal pollution, harming aquatic life.
Mining's Environmental Degradation
The metal value chain begins with the mining of raw materials, such as iron ore for steel and bauxite ore for aluminum. Mining has its own environmental costs, including air pollution and significant water contamination.
A major risk associated with both copper and coal mining is acid mine drainage, a process in which waste rock reacts with air and water to form sulfuric acid. This acidic runoff can devastate aquatic life for thousands of years.
For aluminum, the refining of bauxite ore produces a hazardous, high-volume byproduct known as "red mud." This toxic sludge is stored in vast ponds, posing a severe risk of contaminating soil and water.
How key industrial metals are made and their impacts
Understanding a product's environmental footprint requires knowing how its core materials are made. For metals, the production path, particularly the distinction between primary (derived from ore) and secondary (derived from scrap), is the primary factor determining their carbon footprint.
Steel production and its carbon footprint
- The High-Carbon Path (BF-BOF): The traditional Blast Furnace-Basic Oxygen Furnace route makes up about 70% of global steel production. It creates "virgin" steel from iron ore and is extremely carbon-intensive because it uses coke, derived from coal, as a fuel and a chemical reducing agent. This process releases about 2.2 tonnes of CO₂ equivalent (tCO₂e) for every tonne of crude steel.
- The Low-Carbon Path (EAF): The modern Electric Arc Furnace route primarily recycles existing steel scrap. By melting scrap with electricity, it bypasses the need for coal. This results in a much lower carbon footprint, averaging around 0.5 tCO₂e per tonne of steel, a reduction of over 75%. The primary source of emissions is the electricity used to power the furnace.
Aluminum: A lightweight metal with a heavy energy cost
Aluminum is critical for aerospace, automotive, and packaging industries. However, its primary production is incredibly energy-intensive.
- Primary Production (Hall-Héroult Process): Virgin aluminum is made using the Hall-Héroult process, where a powerful electric current separates alumina (aluminum oxide) from molten cryolite. This process consumes a substantial amount of electricity. The carbon anodes used in the process are consumed, releasing not only CO₂ from the electricity generation but also potent perfluorocarbons (PFCs). These PFCs have a global warming potential thousands of times higher than CO₂.
- Secondary Production (Recycling): Recycled aluminum plays a crucial role in the industry's decarbonization efforts. It requires only 5% of the energy needed for primary production, dramatically lowering its carbon footprint.
Copper: The conductor of the clean transition
Copper's high conductivity makes it essential for electrification. However, its extraction has significant environmental costs.
- Primary Production (Smelting): Copper is typically extracted from ore through a process that involves crushing, concentrating, smelting, and refining. Smelting uses immense heat, often generated by fossil fuels, to separate the metal from its ore. This process can release large amounts of sulfur dioxide (SO₂), a key contributor to acid rain, along with heavy metal pollutants like lead and arsenic.
- Secondary Production (Recycling): Like aluminum, copper is highly recyclable and retains its quality. Recycling copper uses up to 85% less energy than primary production.
Other critical metals
- Zinc: Used for galvanizing steel, zinc production from mining and smelting can release the metal into water systems. In high concentrations, zinc is toxic to marine life, like phytoplankton and corals.
- Nickel: Vital for batteries, nickel production is an energy-intensive process. Processing laterite ores, common in tropical regions, requires significantly more energy and chemicals than processing sulfide ores, leading to a much higher carbon footprint, often 4 to 5 times greater.
- See lithium’s environmental impact and the paradox of clean energy.
Decarbonization pathways for the metals industry
The metals industry is changing. Innovation is underway to transform this sector. Several key technologies are leading the way toward a low-carbon future for steel, aluminum, and other metals.
The power of recycling
The quickest way to reduce a metal's carbon footprint is to use recycled scrap. Steel, aluminum, and copper are infinitely recyclable without losing quality.
However, the global supply of scrap is limited and cannot meet the world's growing demand. This "scrap gap" means producing virgin metal is still necessary, requiring new, cleaner primary production methods.
Breakthroughs in technology
- Green Hydrogen for Steel: Green hydrogen, produced using renewable energy, can replace coal in the ironmaking process, as demonstrated by the HYBRIT project. The only byproduct is water, offering a path to near-zero emission steel.
- Inert Anodes for Aluminum: Developing inert, or non-carbon, anodes for the Hall-Héroult process is a major focus. These anodes would release oxygen instead of CO₂, eliminating the direct process emissions from smelting.
- Carbon Capture (CCUS): For existing plants, Carbon Capture, Utilization, and Storage (CCUS) is a transitional technology that can capture up to 90% of a plant's CO₂ emissions. However, it is costly and energy-intensive.
How to calculate a metal's carbon footprint
For any business that uses metals, calculating the Product Carbon Footprint (PCF) is becoming increasingly necessary. It is a key part of risk management and meeting market demands.
1. Define Your Goal and Scope
First, establish the purpose of the calculation (e.g., internal benchmarking, regulatory compliance). Define the functional unit (e.g., one tonne of I-beam) and the lifecycle boundaries (cradle-to-gate is most common for B2B).
2. Gather Your Activity Data
The accuracy of a PCF depends on the quality of the data. You will need a detailed Bill of Materials (BOM), information on supplier locations, your own energy consumption data, and transportation logistics.
3. Identify the Production Pathway
A metal product's carbon footprint is primarily determined by its production method. The emissions difference between primary (from ore) and secondary (from scrap) production is huge.
The most important question to ask your supplier is:
"Was this metal produced via a primary or secondary (recycled) route?"
4. Apply Emission Factors and Calculate
Once you have your data, you use emission factors to convert it into emissions. The basic formula is:
Emissions = Activity Data × Emission Factor
5. Analyze and Act
The total PCF is just the start. Hotspot Analysis helps identify the largest contributors to your product's footprint, allowing you to create targeted strategies, such as switching to a lower-carbon supplier.
How Arbor helps you manage your metal carbon footprint
Understanding the carbon footprint of your products is complex, but it is quickly becoming a requirement for doing business. Regulations require it, and customers are demanding it. This is where Arbor can help.
Arbor’s carbon accounting platform is designed to simplify the process of calculating Product Carbon Footprints (PCFs) for items containing steel, aluminum, and other metals.
Instead of spending months on manual calculations, Arbor's platform automates the work, delivering accurate results quickly. We can process thousands of products, giving you a clear view of your entire portfolio.
With Arbor, you can:
- Get Accurate PCFs Fast: Use your existing Bill of Materials and supply chain data to generate precise, region-specific carbon footprints.
- Identify Hotspots: Our analysis tools pinpoint the biggest emission sources in your supply chain, so you know exactly where to focus your reduction efforts.
- Meet Regulatory Demands: Easily generate the data required for compliance with regulations such as the EU's CBAM.
- Make Smarter Sourcing Decisions: Compare the carbon footprint of different suppliers and materials to build a more resilient and lower-impact supply chain.
By turning complex data into clear, actionable insights, Arbor gives you the information you need to effectively manage your emissions.
Start measuring your product’s carbon footprint today.
How regulations like CBAM impact metal imports
Measuring a product's carbon footprint was once voluntary. Now, regulations like the European Union's Carbon Border Adjustment Mechanism (CBAM) are making it a requirement for iron, steel, and aluminum.
CBAM puts a price on the carbon emitted during the production of goods imported into the EU. Starting in 2026/2027, importers will need to buy "CBAM certificates" to cover the embedded emissions of their goods.
This forces transparency in global supply chains. EU importers need primary emissions data from their producers. If they don't have it, they face high default values.
This creates a powerful financial incentive for non-EU producers to measure, verify, and reduce their emissions to remain competitive in the EU market.
Summary
The metals industry faces a significant challenge in reducing its environmental impact. The path forward involves a shift from high-carbon primary production to cleaner methods, driven by recycling, clean energy, and new technologies such as green hydrogen and inert anodes.
For businesses that use steel and aluminum, the operating environment has changed. Understanding and managing a product's carbon footprint is now a core business necessity, driven by regulations such as CBAM and increasing market pressure.
Progress is built on credible, transparent data. The first step for any company is to measure its metal-related carbon footprint. By doing this, businesses can reduce risk, ensure compliance, and build a more resilient and competitive operation.
Measure your carbon emissions with Arbor
Simple, easy carbon accounting.
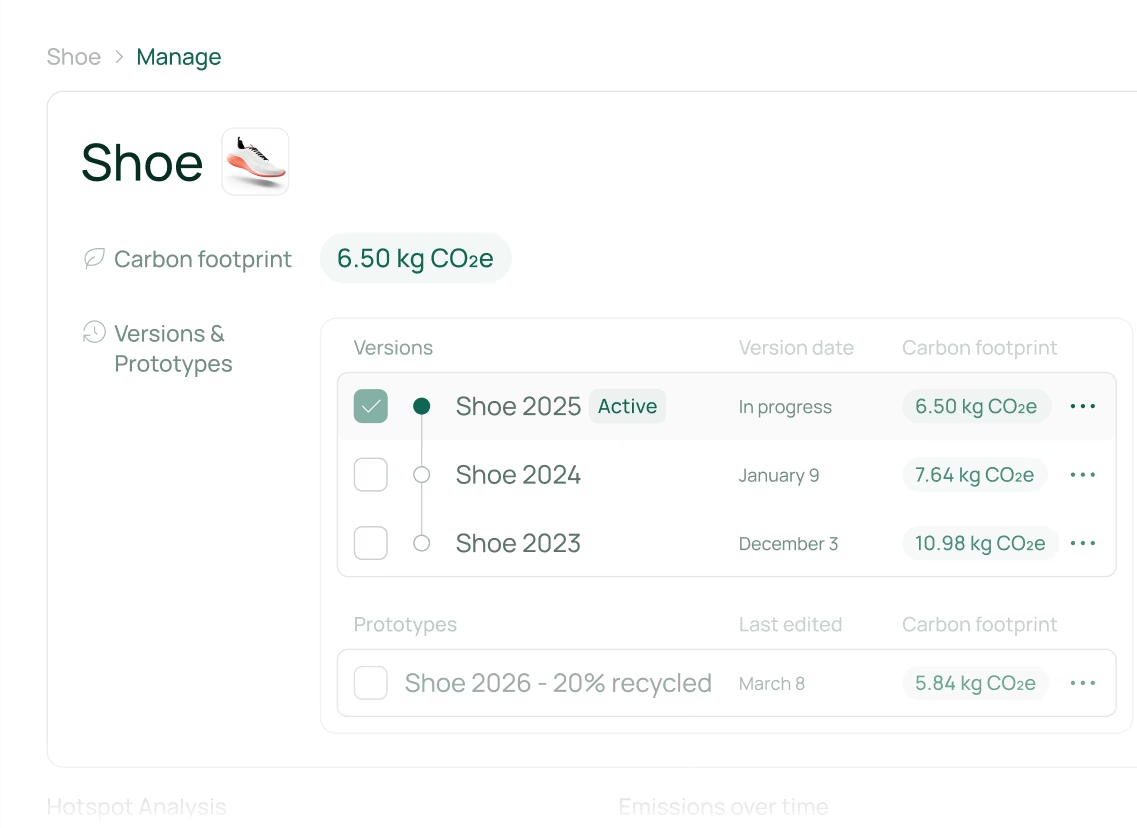